Efficient Strategies for Attaining Ideal Foam Control in Chemical Production
Effective foam control is an important aspect of chemical manufacturing that can significantly influence manufacturing effectiveness and item quality. By comprehending the devices of foam formation and picking suitable anti-foaming representatives, producers can take aggressive actions to minimize too much foam. Furthermore, the execution of procedure optimization techniques and advanced surveillance systems plays an essential duty in keeping ideal operating conditions. However, the subtleties of these strategies can differ commonly throughout different applications, increasing essential concerns concerning best methods and real-world executions that merit additional expedition.
Comprehending Foam Development

Surfactants, or surface-active agents, reduce the surface stress of the liquid, facilitating bubble stability and advertising foam generation. Additionally, frustration or mixing procedures can boost bubble development, frequently exacerbating foam problems. The features of the liquid medium, including viscosity and density, additional influence foam behavior; for instance, more viscous fluids tend to trap air better, bring about enhanced foam security.
Recognizing these essential facets of foam formation is crucial for reliable foam control in chemical manufacturing. By acknowledging the problems that promote foam development, producers can apply targeted techniques to reduce its unfavorable effects, therefore enhancing manufacturing procedures and making certain regular item top quality. This foundational knowledge is essential before exploring certain approaches for controlling foam in commercial setups.
Choice of Anti-Foaming Agents
When selecting anti-foaming agents, it is necessary to consider the particular attributes of the chemical procedure and the sort of foam being created (Foam Control). Numerous aspects influence the efficiency of an anti-foaming representative, including its chemical structure, temperature level security, and compatibility with other process materials
Silicone-based anti-foams are widely made use of as a result of their high effectiveness and wide temperature level range. They work by decreasing surface area stress, enabling the foam bubbles to integrate and break more easily. However, they might not be suitable for all applications, especially those including delicate formulations where silicone contamination is a concern.
On the other hand, non-silicone representatives, such as mineral oils or organic substances, can be useful in details scenarios, specifically when silicone deposits are unfavorable. These agents have a tendency to be less effective at greater temperatures however can provide reliable foam control in various other problems.
Additionally, comprehending the foam's origin-- whether it arises from oygenation, agitation, or chain reactions-- overviews the choice procedure. Checking under real operating conditions is critical to guarantee that the picked anti-foaming agent fulfills the unique needs of the chemical manufacturing process properly.
Refine Optimization Methods
Reliable foam control is a vital facet of optimizing chemical production procedures. To enhance efficiency and lessen manufacturing prices, producers must execute targeted procedure optimization techniques. One vital method includes readjusting mixing rates and configurations. By fine-tuning these specifications, drivers can lower disturbance, therefore decreasing foam development during mixing.
In addition, managing temperature level and pressure within the system can considerably impact foam generation. Reducing the temperature level might minimize the volatility of specific parts, leading to lowered foam. Also, keeping optimum pressure degrees assists in mitigating excessive gas launch, which contributes to foam stability (Foam Control).
One more efficient approach is the calculated addition of anti-foaming agents at critical points of the procedure. Cautious timing and dose can additional resources ensure that these agents properly reduce foam without interrupting other process criteria.
In addition, including a systematic assessment of resources properties can assist determine naturally lathering substances, permitting preemptive measures. Lastly, performing routine audits and process evaluations can expose inadequacies and locations for enhancement, enabling constant optimization of foam control methods.
Tracking and Control Solution
Surveillance and control systems play a critical duty in maintaining optimum foam monitoring throughout the chemical manufacturing procedure. These systems are vital for real-time monitoring and adjustment of foam degrees, guaranteeing that manufacturing efficiency is made the most of while minimizing disruptions brought on by excessive foam development.
Advanced sensing units and instrumentation are used to spot foam thickness and height, giving vital information that notifies control find formulas. This data-driven strategy enables for the timely application of antifoaming agents, guaranteeing that foam degrees continue to be within appropriate limits. By integrating monitoring systems with process control software program, producers can carry out computerized feedbacks to foam fluctuations, decreasing the requirement for manual treatment and boosting operational uniformity.
In addition, the combination of equipment understanding and anticipating analytics right into keeping an eye on systems can assist in aggressive foam management. By analyzing historic foam data and operational specifications, these systems can forecast foam generation patterns and advise preemptive measures. Routine calibration and maintenance of monitoring devices are vital to ensure precision and reliability in foam discovery.
Inevitably, reliable tracking and control systems are important for enhancing foam control, promoting safety and security, and boosting overall performance in chemical production atmospheres.
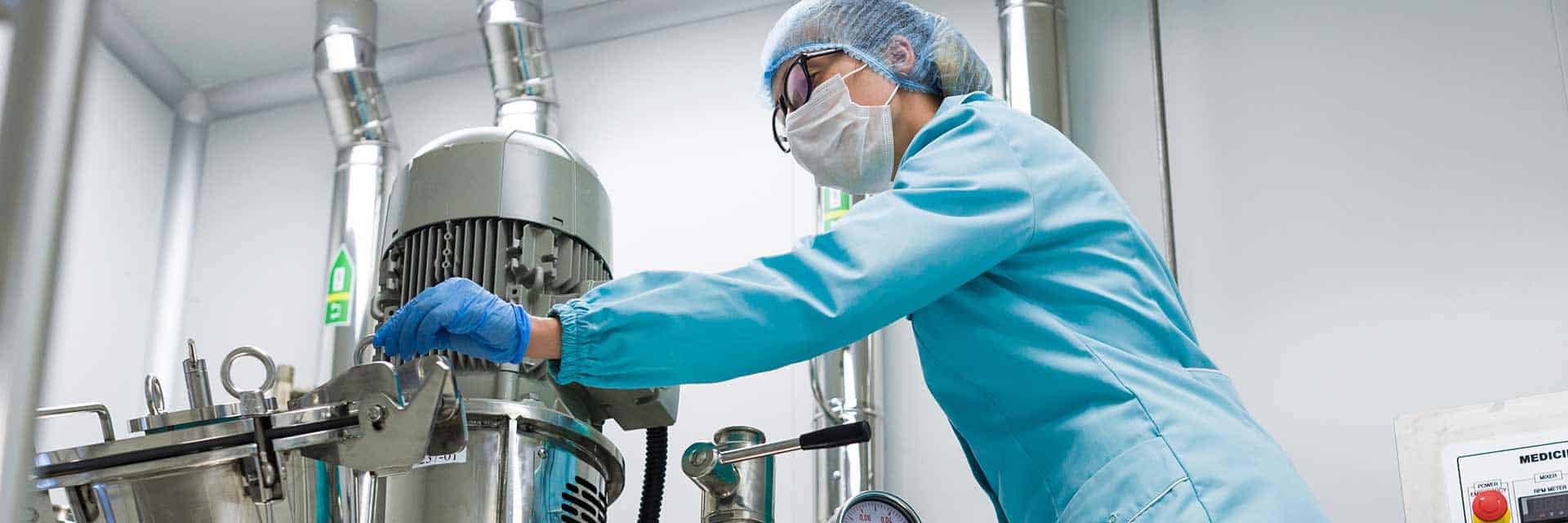
Case Studies and Best Practices
Real-world applications of surveillance and control systems highlight the value of foam administration in chemical manufacturing. A remarkable situation study includes a large-scale pharmaceutical producer that implemented an automated foam detection system. By incorporating real-time tracking with anticipating analytics, the facility lowered foam-related manufacturing downtime by 30%. The data-driven strategy permitted timely treatments, guaranteeing constant product top quality and operational effectiveness.
One more exemplary instance originates from a petrochemical firm that embraced a mix of antifoam agents and procedure optimization strategies. By analyzing foam generation patterns, the organization tailored its antifoam dosage, leading to a 25% reduction in chemical use and considerable cost financial savings. This targeted method not only reduced foam interference yet likewise enhanced the overall stability of the manufacturing procedure.

Conclusion
Finally, accomplishing optimal foam control in chemical production demands a comprehensive approach incorporating the option of appropriate anti-foaming representatives, execution of procedure optimization strategies, and the combination of sophisticated monitoring systems. Routine audits and training additionally improve the efficiency of these approaches, fostering a society of continuous renovation. By addressing foam formation proactively, producers can considerably boost production performance and product high quality, ultimately adding to more affordable and sustainable operations.
By comprehending the mechanisms of foam formation and choosing suitable anti-foaming agents, producers can take positive steps to mitigate find out here now excessive foam. The characteristics of the liquid tool, consisting of thickness and density, additional influence foam habits; for example, more viscous fluids have a tendency to trap air extra efficiently, leading to raised foam stability.
Recognizing these essential aspects of foam development is vital for efficient foam control in chemical manufacturing. By examining historic foam information and operational criteria, these systems can anticipate foam generation patterns and suggest preemptive procedures. Foam Control. Normal audits of foam control gauges make sure that procedures continue to be maximized, while cultivating a society of proactive foam monitoring can lead to lasting renovations across the manufacturing spectrum